3D printing has revolutionized the way we prototype and manufacture objects, making it accessible to hobbyists, professionals, and industries alike. However, like any technology, FDM printing is not without its challenges. This article aims to address common FDM 3D printing issues and provide practical solutions to help users achieve better results.
We’ll guide you through the intricacies of troubleshooting extrusion problems, combating filament jams that can disrupt your printing flow, and addressing issues like layer shifting and inconsistent layer heights that might be affecting the overall quality of your prints. Whether you’re grappling with bed adhesion problems or trying to decipher the mysteries behind nozzle clogs, our guide provides clear and practical solutions to empower you with the skills needed to achieve stellar results in your 3D printing endeavors.
1. Layer Adhesion Problems:
Issue: Poor layer adhesion can result in weak prints.
Solutions:
- Adjust Print Temperature: Ensure the print temperature falls within the recommended range for the filament. Too high or too low temperatures can affect layer bonding.
- Optimize Bed Leveling: A well-leveled bed ensures consistent layer adhesion. Regularly check and recalibrate the bed to maintain an even first layer.
- Experiment with Layer Heights: Varied layer heights can affect adhesion. Experiment with different layer heights to find the optimal setting for your specific filament and print.
2. Warped Prints:
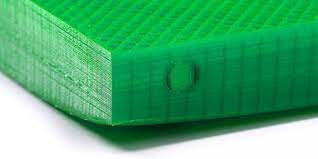
Issue: Corners lifting or warping during printing.
Solutions:
- Use Heated Bed: Employ a heated bed to improve adhesion and minimize warping. Experiment with different bed temperatures based on the filament requirements.
- Enhance Bed Adhesion: Employ a brim or raft to provide more surface area for the print to adhere to the bed. Additionally, consider using adhesion aids like hairspray or glue stick.
- Enclosure: Create a controlled printing environment by enclosing the printer, reducing temperature fluctuations and minimizing the chances of warping.
3. Extrusion Issues:
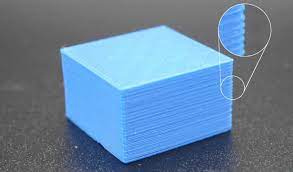
Issue: Uneven extrusion, under-extrusion, or over-extrusion.
Solutions:
- Regular Nozzle Maintenance: Clean the nozzle regularly to prevent clogs and ensure smooth filament flow.
- Extruder Calibration: Calibrate the extruder steps/mm to ensure accurate filament feeding.
- Filament Inspection: Check the filament for inconsistencies or signs of moisture. Dry filament thoroughly before use if necessary.
- Adjust Flow Rate: Fine-tune the flow rate settings in your slicer to control the amount of filament extruded.
4. Stringing and Oozing:
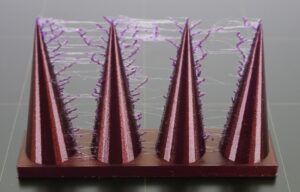
Issue: Thin strands of filament between printed parts.
Solutions:
- Retraction Settings: Optimize retraction settings to minimize filament oozing during non-print moves.
- Temperature Adjustment: Lower the print temperature to reduce the likelihood of stringing.
- Travel Speed: Experiment with travel speeds to find the right balance between minimizing stringing and maintaining print quality.
- Combing Mode: Use combing mode to limit nozzle movement within the printed area, minimizing stringing during travel moves.
5. Layer Shifting:
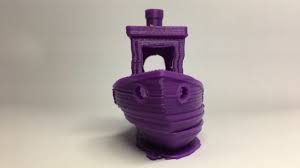
Issue: Layers not aligning, causing a misshapen print.
Solutions:
- Stable Printer Placement: Ensure the printer is on a stable surface to prevent vibrations that can lead to layer shifting.
- Belt Tightening: Check and tighten the belts to maintain proper tension and prevent slipping.
- Lubrication: Regularly lubricate moving parts, such as rods and bearings, to ensure smooth movement without resistance.
- Power Supply Stability: Verify that the power supply is stable, as fluctuations can result in unexpected movements.
6. Z-Wobble:
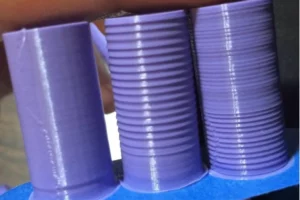
Issue: Visible artifacts in the Z-axis.
Solutions:
- Leadscrew Couplings: Ensure Z-axis leadscrew couplings are tightened securely to eliminate wobbling.
- Smooth Rod Movement: Check for any obstructions or misalignments that may impede smooth rod movement in the Z-axis.
- Frame Stability: Reinforce the Z-axis frame to minimize any unwanted movement or flexing during printing.
7. Filament Jamming:
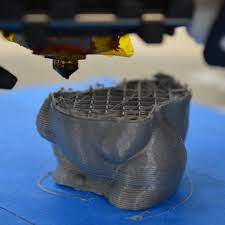
Issue: Filament getting stuck in the extruder or nozzle.
Solutions:
- Nozzle Cleaning: Regularly clean the nozzle to remove any accumulated debris or burnt filament.
- Maintain Hotend Temperature: Ensure the hotend maintains a consistent temperature to prevent filament from solidifying prematurely.
- Quality Filament: Use high-quality filament to reduce the chances of impurities causing jams.
- Filament Filter: Install a filament filter to catch and remove any debris before it reaches the hotend.
8. Inconsistent Layer Heights:
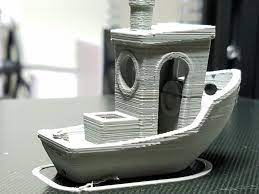
Issue: Variances in layer height leading to uneven prints.
Solutions:
- Z-axis Calibration: Calibrate the Z-axis steps/mm to ensure accurate layer height.
- Bed Leveling: Regularly check and maintain bed leveling for uniform layer adhesion.
- Mechanical Inspection: Inspect mechanical components for any issues that may affect the Z-axis movement.
9. Print Not Sticking to the Bed:
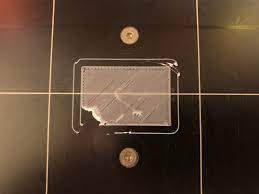
Issue: First layers not adhering properly.
Solutions:
- Accurate Bed Leveling: Ensure precise bed leveling to achieve proper first layer adhesion.
- Clean Bed Surface: Keep the bed surface clean from dust or residues that may hinder adhesion.
- Nozzle Height Adjustment: Fine-tune the nozzle height for optimal first layer adhesion.
- Heated Bed and Adhesion Aids: Utilize a heated bed and consider using adhesion aids like hairspray or glue stick to enhance bed adhesion.
10. Nozzle Clogs:
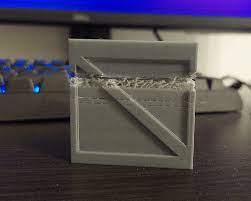
Issue: Material buildup causing the nozzle to clog.
Solutions:
- Regular Nozzle Cleaning: Implement a routine nozzle cleaning schedule to prevent clogs.
- High-Quality Filament: Use reputable and high-quality filament to minimize the presence of contaminants.
- Avoid Excessive Temperatures: Avoid printing at temperatures beyond the recommended range to prevent filament degradation.
- Filament Filter: Install a filament filter to capture any debris or impurities before they reach the nozzle.